Le funi di trazione in acciaio sono, fra gli organi di un impianto di sollevamento, uno dei componenti da verificare con periodicità ed attenzione. Vediamone insieme le caratteristiche, gli indici di usura ed i più moderni metodi di controllo
L’importanza di un buon grado di conservazione delle funi in acciaio è di per se ampiamente noto anche fra i non addetti, e raramente i proprietari degli impianti trascurano la necessità di operarne la sostituzione quando segnalata dal proprio manutentore. Ben pochi tuttavia conoscono le caratteristiche di questo importante componente, le modalità di verifica, le condizioni che ne impongono la sostituzione e le norme tecniche dedicate. Facciamo chiarezza.
Le caratteristiche costruttive di una fune per ascensori
Una tipica fune metallica è costituita da numerosi fili singoli, formati e costruiti in modo da poter lavorare in stretta aderenza. Quando la fune si piega ognuno dei suoi numerosi fili singoli scivola a sistemarsi nella piega, compensando la differenza di lunghezza fra la piega esterna e quella interna. Più brusca è la piega, maggiore il movimento.
La costruzione della fune è caratterizzata da tre componenti fondamentali:
- I fili singoli, che formano i trefoli fornendo nell’insieme la resistenza della fune;
- I trefoli, formati ad elica attorno all’anima centrale;
- L’anima della fune, tessile o metallica anch’essa, che forma il sottofondo per la costruzione dei trefoli;
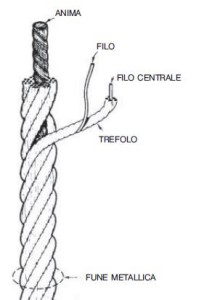
Alcune tipiche formazioni della fune in ambito ascensoristico sono, ad esempio, 6×19 FC (6 trefoli preformati in una costruzione costituita da 114 fili totali, ovvero 9+9+1 su ogni trefolo) od 8×19 FC (8 trefoli preformati in una costruzione costituita da 152 fili totali).
Le lettere FC indicano la natura dell’anima centrale, in questo caso tessile costituita da fibre naturali o sintetiche. La sigla IWRC indicherebbe diversamente l’utilizzo di un’anima centrale costituita da fune in acciaio. Il senso di avvolgimento della fune, nella nomenclatura prevista dalle norme tecniche, è riferito ai fili esterni rispetto ai trefoli, ed ai trefoli rispetto alla fune: “Z” stà ad indicare l’avvolgimento destro, “S” l’avvolgimento sinistro. Nel caso di funi a trefoli sono inoltre impiegate due lettere con caratteri di differente altezza. La prima lettera, più piccola, indica il senso di cordatura dei fili esterni nei trefoli, la seconda, di maggiori dimensioni, indica il senso di cordatura dei trefoli nella fune.
Realizzati in acciaio ad alto contenuto di carbonio i fili delle funi metalliche sono disponibili in vari “gradi” ad ognuno dei quali corrisponde una specifica resistenza della fune metallica. Secondo la secondo UNI EN 12385-5:2004, versione ufficiale in lingua italiana della norma europea EN 12385-5 (edizione ottobre 2002 + AC:2005), che specifica i materiali particolari, i requisiti di fabbricazione e di prova per le funi a trefoli per compiti di sospensione, compensazione e limitazione per ascensori a frizione e idraulici che si muovono lungo guide, “il grado definisce il valore di resistenza alla trazione dei fili interni ed esterni della cordatura“. Il “grado” definisce inoltre il carico minimo di rottura della fune, espresso in Newton, normalmente pari a 1570 N/mm² nelle normali funi a singola classe di resistenza.
Funi a singola classe di resistenza e funi a resistenza differenziata
Oltre alle usuali funi a singola classe di resistenza, dotate come detto di un carico minimo di rottura di 1570 N/mm², pari a circa 160 Kg/mm², esistono sul mercato funi a doppia classe di resistenza, anche dette a trazione duale od a resistenza differenziata. In queste funi, indicate con grado 1370/1770, i fili esterni dei trefoli esterni hanno un carico minimo di rottura pari a 1370 N/mm² ed i fili interni della fune un carico di rottura pari a 1770 N/mm².
L’utilizzo di funi a doppia classe di resistenza, grazie al grado differenziato con maggiore malleabilità esterna dei trefoli, garantisce una minore usura delle pulegge di trazione sui macchinari di sollevamento, con conseguenti benefici in termini di durata e minori costi di mantenimento
In entrambe i casi le funi utilizzate negli ascensori sono calcolate con un coefficiente 12, ovvero il carico di rottura dovrà essere minimo 12 volte il carico totale dell’impianto gravante sulle funi stesse, o 16 volte per vecchi impianti ancora dotati di due sole funi.
Quando sostituire le funi di trazione
La vita media di una fune può variare considerevolmente in funzione del carico a cui è sottoposta, delle condizioni di utilizzo e, chiaramente, delle sue caratteristiche, in un range temporale che và generalmente dai dieci ai trent’anni. Tuttavia stabilire con precisione se e quando una fune sia ormai obiettivamente da sostituire non è affatto semplice, ed in genere è affidata ad una valutazione empirica sul numero dei fili esterni rotti, sulla riduzione del diametro e sulla visiva corrosione.
La normativa in merito
Al riguardo esistono precise normative delle quali tener conto nella valutazione del grado di usura di una fune, attraverso l’esame del numero di fili rotti, per determinare la necessità di provvedere alla sua sostituzione. Il DPR 29 maggio 1963 n. 1497 nell’articolo 39 ( Ricambio delle funi o delle catene portanti) dispone che:
- Le funi portanti che mostrano degradazione o logoramento evidenti, o numero eccessivo di fili rotti, devono essere sostituite.
- Nel caso di incertezze sulla necessità di sostituire le funi portanti, queste devono essere sostituite quando nel tratto più deteriorato, in una lunghezza uguale a 10 diametri della fune per funi con sei trefoli e a 8 diametri della fune per funi con otto trefoli, i fili rotti visibili abbiano una sezione complessiva maggiore del 10% della sezione metallica totale della fune.
Un’ulteriore ausilio per la valutazione del grado d’usura delle funi arriva nel 1994 con il recepimento della UNI ISO 4344:1992, superata e parzialmente abrogata dalla UNI EN 12385-5:2004, che tuttavia richiama la stessa per il numero ammissibile di fili rotti. Nella tabella a lato, tratta dalla norma suindicata, le indicazioni per la sostituzione delle funi in funzione del numero di fili rotti per due tipologie di funi. Due ulteriori importanti fattori da tenere in considerazione sono, come anticipato, inerenti l’usura che comporta la riduzione del diametro dei fili e la corrosione. In entrambe i casi, fili il cui diametro è ridotto oltre un certo limite o particolarmente corrosi, devono essere considerati al pari di fili rotti nella valutazione.
In ogni caso la fune deve essere rimossa dal servizio e sostituita quando:
- Il diametro si è ridotto del 10%;
- Un trefolo sia completamente rotto od in qualche punto si sia ridotta la sua sezione del 40%;
- Sono presenti deformazioni, ammaccature o torsioni;
- Fuoriesce l’anima;
- Pur essendo la fune in tensione uno o più trefoli risultino lenti;
Di seguito vengono riportati alcuni dei più comuni segni di decadimento tratti dalla suindicata norma UNI ISO 4344:1992
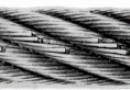
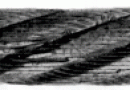
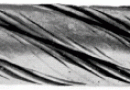
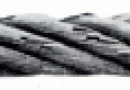
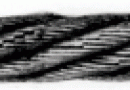
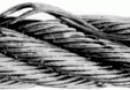
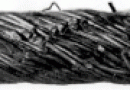
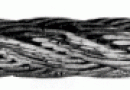
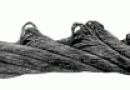
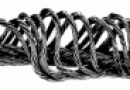
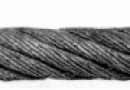
I moderni metodi di valutazione: L’analisi magneto-induttiva
Sebbene in molti dei casi suesposti il degrado della fune non lasci dubbi circa la necessità di una quanto più sollecita sostituzione, nella realtà dei fatti è piuttosto raro che un impianto regolarmente manutenuto presenti simili condizioni. Determinare con oggettività quando la fune sia ormai prossima alla conclusione del suo ciclo vitale può quindi, come anticipato, risultare estremamente arduo, soprattutto nei casi in cui il deterioramento sia maggiormente concentrato nell’area interna con un contenuto numero di fili esterni visibili.
Le moderne tecnologie tuttavia consentono oggi esami non distruttivi della fune, con una significativa valenza predittiva. In particolare fra questi l’analisi magneto-induttiva, mutuata dal settore funiviario, attualmente sempre più diffusa nell’ambito del sollevamento dei carichi e degli ascensori. L’innovativo screening è caratterizzato dall’utilizzo di una testa di misura appositamente ingegnerizzata per il controllo di apparecchiature multifune in abbinamento ad uno specifico software d’interpretazione del segnale.
Gli strumenti attualmente disponibili sul mercato sono in grado di fornire due diversi specifici segnali rispettivamente denominati “Localized Fault” (LF) e “Loss of Metallic Area” (LMA). Il primo, che fornisce un’indicazione qualitativa dello stato della fune e dipendente dalla profondità del difetto, è utile a determinare quantità e rilevanza del numero di fili rotti, mentre il secondo, in grado di quantificare in modo proporzionale la perdita dell’area equivalente associata al danno, offre una rilevazione dei difetti non localizzati dovuti, ad esempio, alla corrosione. La valenza di queste valutazioni oggettive se paragonate ai consueti metodi di esame, basate sull’osservazione visiva e sul conteggio dei fili rotti “esterni” con l’ausilio di una tavoletta in legno a contrasto delle funi durante il movimento dell’impianto, di per se intuibile, è stata confermata da un’ampio studio condotto dal Politecnico di Torino su un vasto campione d’esame che ha confermato la validità predittiva del metodo e nel contempo fornito un’inattesa visione d’insieme.
Lo studio, condotto su circa 400 funi d’impianti differenziati per anno d’installazione, numero e tipologia di fune, numero di piani serviti ed ambito d’impiego ha evidenziato infatti situazioni molto particolari, fra le quali anche l’assenza di difetti su impianti con datazione superiore ai venti anni, un risultato che dimostra l’infondatezza delle consuete correlazioni dello stato della fune alla sua età, od in alcuni impianti, anche recenti, una sola fune con numero di difetti nettamente superiore alle altre, esito che attesta come talvolta alcune funi nello stesso insieme siano soggette a maggiore stress ed usura.
La possibilità di intervenire sulla sostituzione della fune all’effettiva occorrenza, e di poter applicare idonei correttivi in caso di usura anomala e non ripartita, si traduce in un oggettivo vantaggio per l’utente finale, sia in termini di sicurezza che di economia nella gestione.
Di seguito alcuni tracciati degli esami condotti con l’individuazione di segnali “LF” (Filo rotto) ed LMA (difetti da corrosione), la testa di misura e la verifica di un impianto ad azionamento oleodinamico